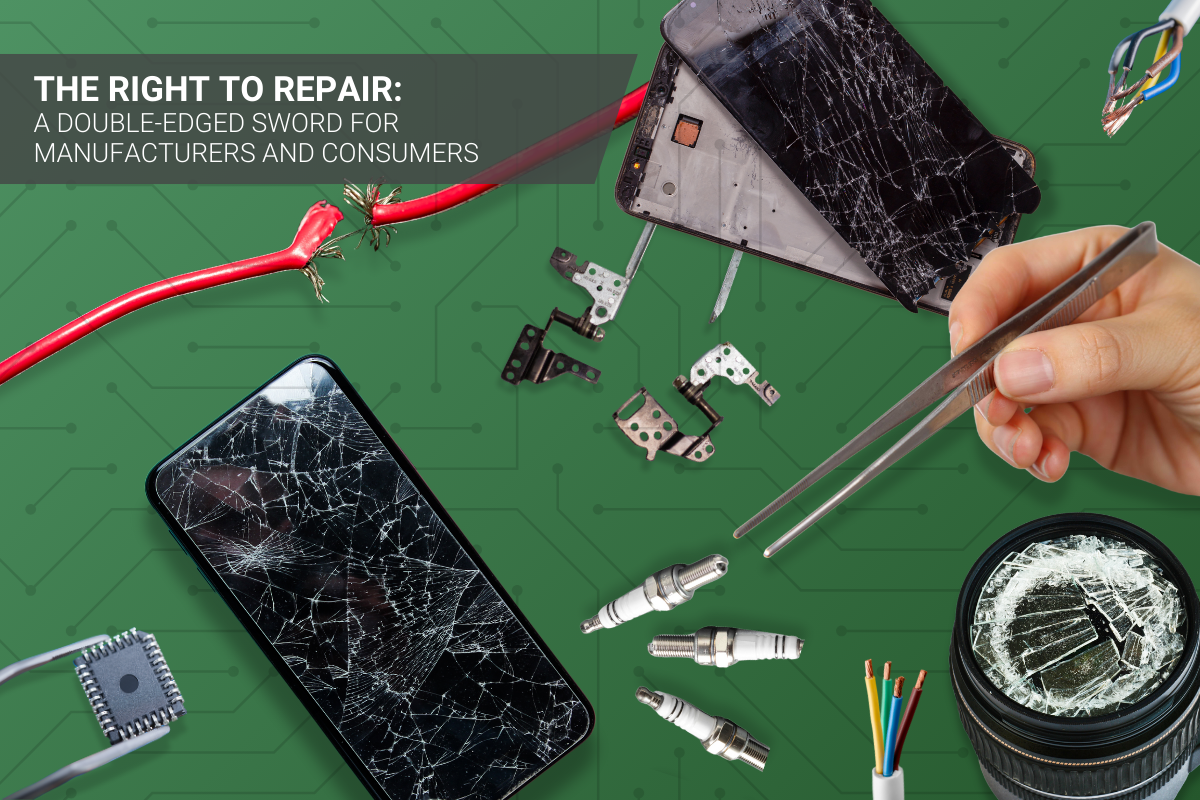
This is the promise of the Right to Repair: a world where items don't merely break and vanish into the void but are afforded a second chance. A place where the idea of repairing is as accessible and commonplace as replacing. A world where the era of costly, inaccessible repairs is behind us, and mending what you own is no longer a burden.
But while this is a win for consumers, it’s an entirely different story for manufacturers and businesses. The Right to Repair doesn’t just empower individuals; it reshapes entire supply chains for companies. Suddenly, businesses are expected to keep extensive inventories of spare parts, ensure timely access to repair manuals, and adapt their supply chains to meet new compliance standards. Imagine the warehouse space, the intricate tracking systems, and the forecasting models required to keep up. For many, it will feel like a complete overhaul of how their products are managed post-sale...
Imagine no longer being a victim of the seemingly endless cycle of "buy, break, and replace." The Right to Repair is here, and it ensures that you have the tools, parts, and knowledge to keep the things you love running smoothly without waste and frustration.
Unpacking the Right to Repair
If you're trying to make sense of the various Right to Repair laws, you're not alone. Whether you're wondering how they affect you as a consumer or what they mean for the future of your business, this article breaks down the complexities of the movement and how you can adapt while benefiting both your customers and the environment.
At its core, the Right to Repair is about giving you more control as an end user. It ensures you can fix and modify your purchases, like when you accidentally drop your phone and shatter its once pristine screen, without being forced into expensive, manufacturer-approved repair options. But it's more than just about fixing what's broken. This movement champions sustainability, affordability, and consumer rights, making repairs more accessible and reducing unnecessary electronic waste.
With greater freedom to choose affordable repair services, you can extend the life of your devices, save money, and contribute to a more sustainable future.

A Global Movement
This legislation doesn't just apply to citizens within the European Union. Around the world, there has been a continuous push for initiatives that promote repairability over replaceability.
In the United States, several states have enacted Right to Repair laws. These laws aim to give individuals and independent repair shops the legal right to access service information, replacement parts, and software tools to fix electronic equipment, be it smartphones, tractors, or medical devices. This reflects a growing recognition of the importance of repairability in promoting sustainability and consumer rights.
Globally, countries are increasingly adopting Right to Repair policies to empower consumers and encourage sustainable practices. The European Union, for example, has implemented regulations requiring manufacturers to make repair information and parts available to consumers and independent repair shops. These initiatives collectively aim to reduce electronic waste, promote sustainability, and give consumers more control over their products.
Why do we need the Right to Repair?
The answer is simple: Repairing should be easy, but it's becoming increasingly difficult. The barriers are mounting: manufacturers restricting access to parts, software locks preventing independent repairs, and repair services that cost nearly as much as replacing the product. These obstacles encourage a throwaway culture, where replacing is favoured over repairing.
The volume of electronic waste is alarming and continues to rise rapidly. The World Health Organisation reported that in 2022, approximately 62 million tonnes of e-waste were generated globally, increasing by 2.6 million tonnes yearly.
According to the Restart Project, the top three barriers to repair include a lack of affordable spare parts, a shortage of tools or documentation necessary for repairs, and the design of products that make them difficult to repair.
Looking under the hood as a business
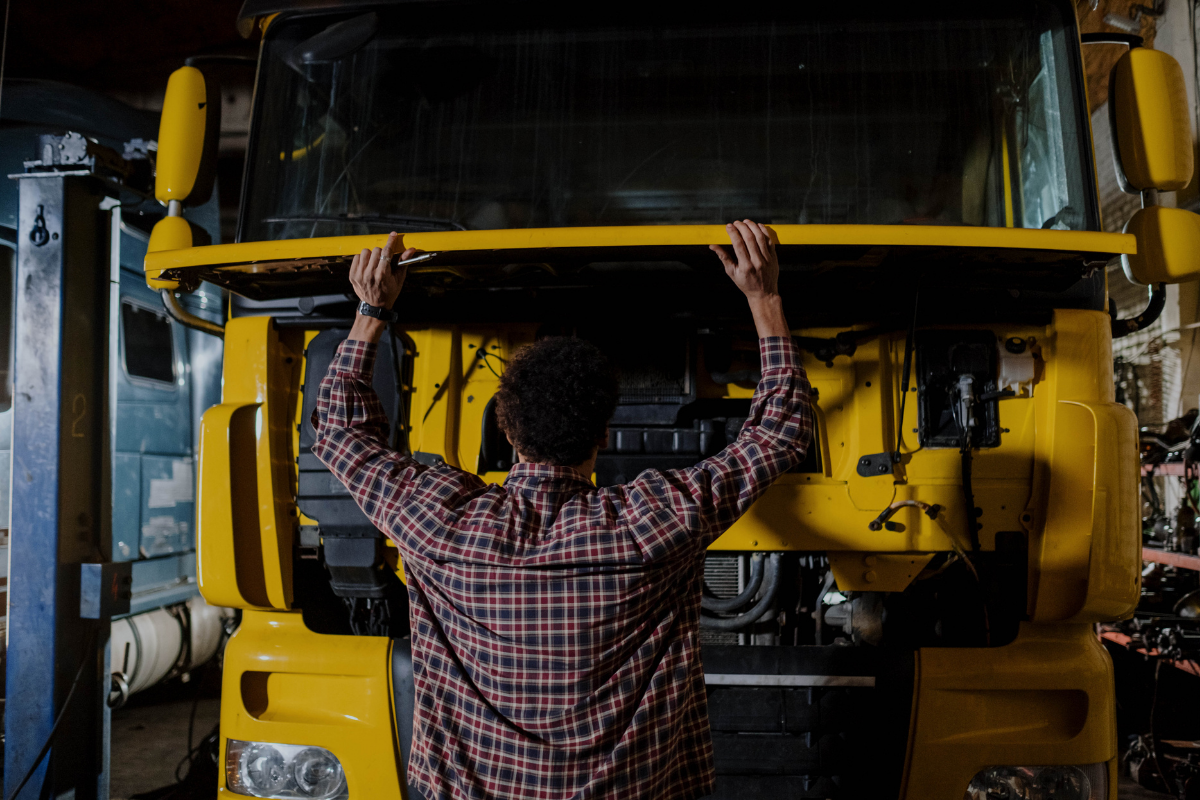
Challenges and Adaptations:
While the Right to Repair legislation is a breath of fresh air for consumers, it presents significant challenges for businesses, particularly manufacturing ones. Companies must now provide access to repair manuals, tools, and spare parts, which can create logistical and financial burdens.
Here are some of the key challenges and strategies businesses are employing to adapt:
Inventory Management and Storage:
One of the biggest hurdles is managing the small parts inventory required for completing repair jobs. Businesses must maintain an extensive inventory of parts, requiring accurate forecasting, regular audits, and efficient categorisation. This can be particularly challenging for companies with a vast product range.
Some companies, like Tesla, have implemented sophisticated inventory management systems to ensure spare parts are always available. By using predictive analytics, they can forecast demand and optimise stock levels, preventing shortages and overstocking.
Cost Implications:
The initial investment required to store parts, purchase tools, and train staff for repairs can be significant. Additionally, maintaining an inventory of small parts incurs ongoing costs, including storage, insurance, and the potential obsolescence of items.
Apple, for example, has had to expand its repair network and parts distribution system to comply with new laws, providing repair manuals and parts to independent repair shops. The recent implementation of the Common Charger Directive in the European Union further highlights the importance of standardisation, forcing manufacturers to align with new cost structures while promoting innovation.
The EU estimates that prematurely discarded products create 35 million tonnes of waste and 261 million tonnes of greenhouse gas emissions yearly.
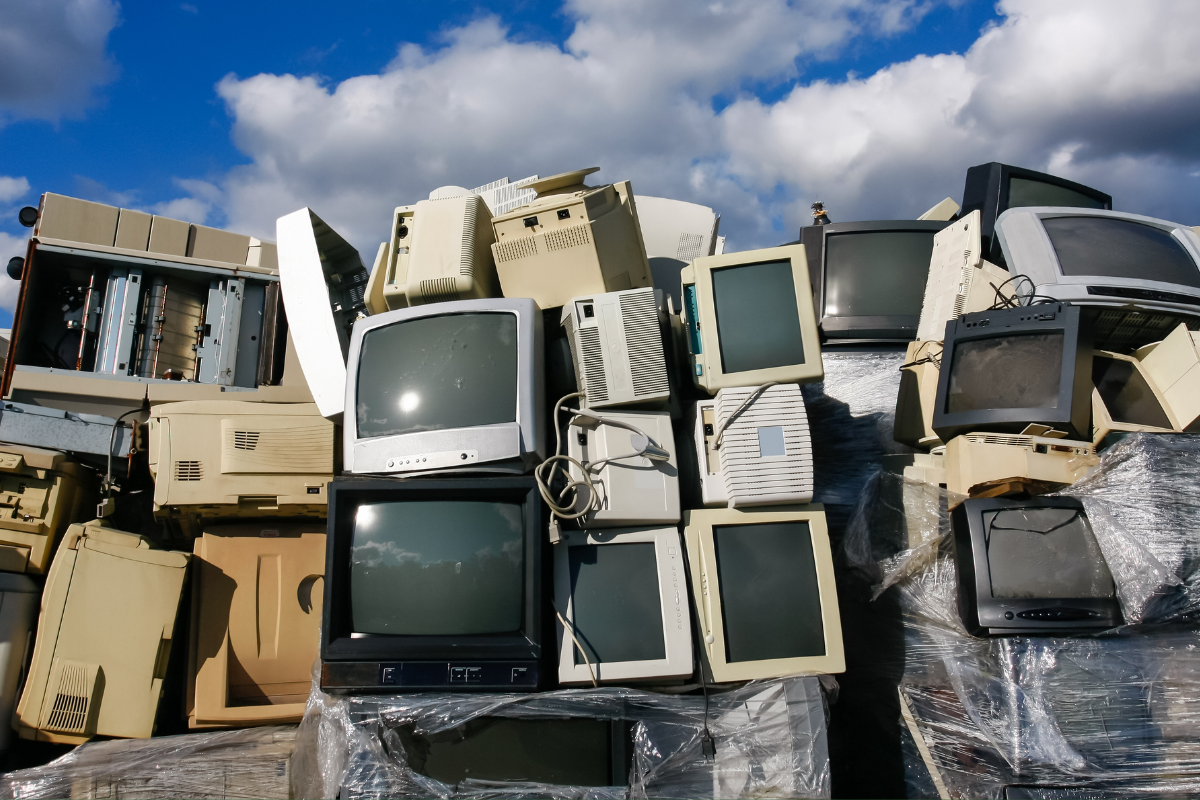
Strategies for Businesses
To navigate these changes, businesses are turning to advanced storage solutions like automated storage and retrieval systems (AS/RS). These systems help organise and quickly access parts, ensuring that repairs are swift and efficient. Maintaining strong relationships with suppliers can also provide a steady flow of spare parts, reducing the risk of stockouts.
Retailers like Currys and John Lewis in the UK are making significant efforts toward accessible repair services, allowing customers to fix their electronics and appliances rather than replacing them entirely.
Looking Ahead
The Right to Repair is here to stay, and while it poses challenges for businesses, it also offers opportunities. Companies that embrace repairability can build stronger customer loyalty, differentiate themselves from competitors, and contribute to a more sustainable future.
If you'd like to learn more about storing small parts and how your business can optimise its inventory management, keep an eye out for our upcoming Small Parts Storage Series, where we'll dive deeper into best practices and innovative storage solutions.