You can have the best pallet racking equipment in the world, but if it doesn’t complement your operation, then efficiency will be compromised. Getting it right is key to successful logistics.
Here, we look at some of the many different types of pallet racking and explain when and how they are best deployed.
What is warehouse pallet racking?
Broadly, warehouse pallet racking comprises a system of metal uprights and cross beams that are used to support the goods being stored.
The type of racking and the way they are configured can be adapted to meet the needs of the warehouse, whether the goods being stored need fast turnaround or longer-term storage; whether they are hand-picked in small amounts or by the pallet-load; or whether the set-up is manually operated or uses robotic automation. They all, however, aim to optimise the space available.
Standard wide aisle pallet racking
Standard wide aisle pallet racking provides your warehousing teams with unrestricted access to all your pallets at all times. The system delivers versatility and assembly as single- or double-depth racks.
Here, the pallets are accessed for picking and replenishing by forklifts, which will have direct and immediate access from the aisle to all the pallet-loads being stored.
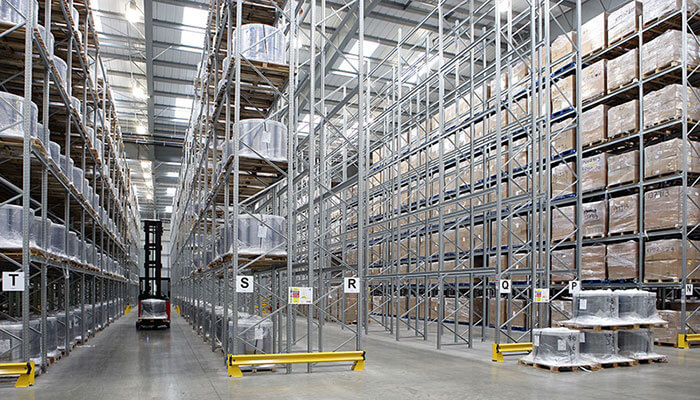
Narrow aisle pallet racking
Narrow aisle pallet racking is ideal for a warehouse where the storage floor space is limited, as it offers high density storage while at the same time allowing for quick order-picking and fast accessibility to every pallet.
Varying shelving heights and depths, together with height-adjustable supporting beams assure maximum flexibility. Narrow aisle pallet racking can represent a space saving of up to 40%. The associated handling equipment is often highly automated to ensure speedy picking, straight from the pallet.
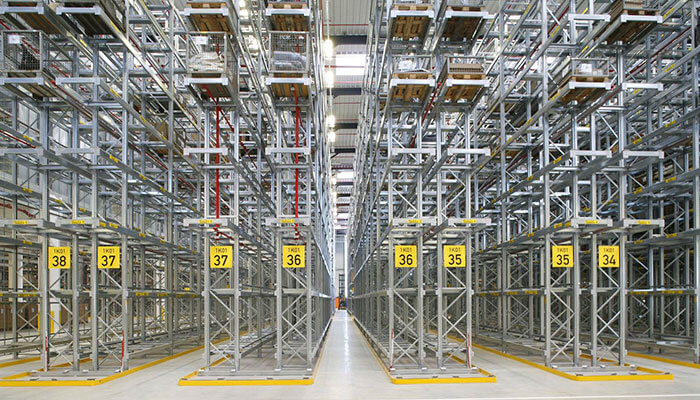
Double deep pallet racking
Double deep pallet racking offers a similar benefit to compact pallet racking, and is a common storage solution. Here, however, there is no direct access to pallets stored at the back. Specially equipped forklifts are needed to access the second pallets, stored to the rear.
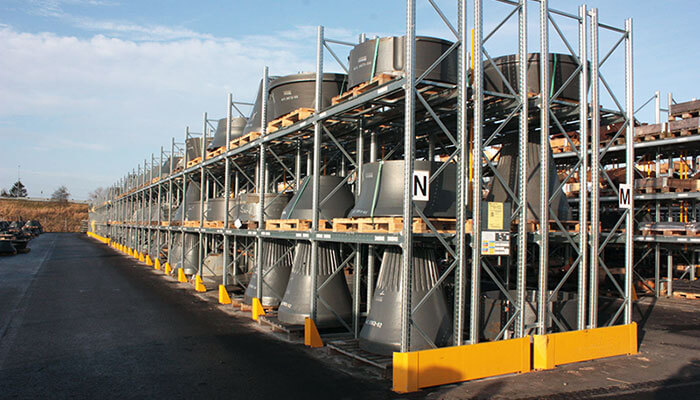
Mobile pallet racking
Mobile pallet racking – or MOVO – is a dynamic solution where the racking moves on rails. The racking can be manually or automatically moved along the rails to open and close aisles, depending where access is needed at any one time. MOVO provides a high density storage solution, taking up to 50% less space than conventional pallet racking.
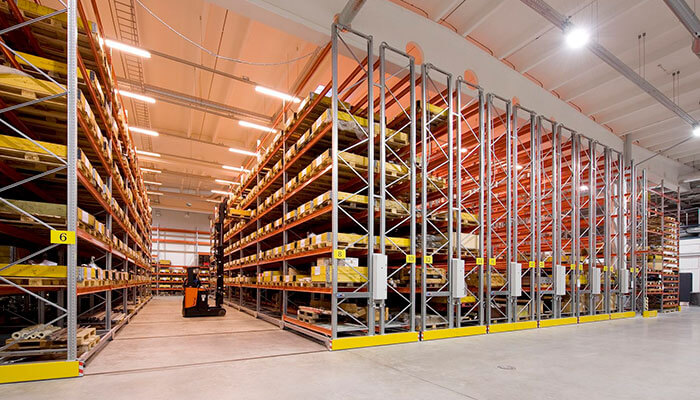
Drive-in pallet racking
Where large quantities of identical goods are being stored, with a low rotation, drive-in pallet racking (or LIFO – last in, first out) is an ideal solution.
Only one aisle, for forklift, is needed, and the last pallet in is the first one to be removed.
Drive-in pallet racking reduces aisle loading and unloading times, yet allows greater access compared to block-stacking.
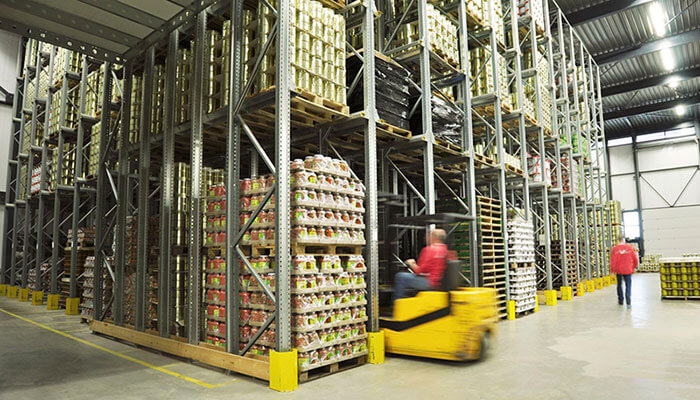
Drive-through pallet racking
Drive through pallet racking needs aisle access from either side of the racking. Using the FIFO (first in, first out) methodology, stock is replenished from one side, and removed from the other.
FIFO is suited to high rotation stock, but the space saving is less that with drive-in racking.
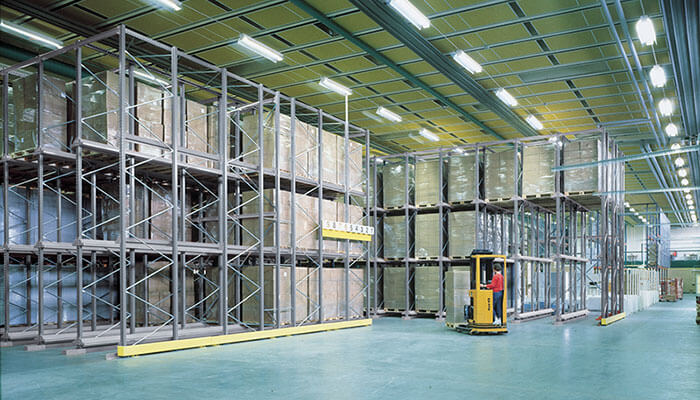
Pallet flow racking
Pallet flow racking is also known as live pallet racking. Pallets travel smoothly on rollers. While the front pallet is removed on the front side of the rack, the rear pallet is held back. Pallet movement is always safe and smooth thanks to automatic braking, along with a combined load guide and end stop unit.
The two main types of live pallet racking are the gravity FIFO live storage system and the push-back LIFO system.
Gravity FIFO live pallet racking system
Here, the loading area is at the opposite end to the picking area, with the pallets travelling along a system of rollers that form a slightly inclined rail. FIFO pallet racking is ideal for products needing perfect stock rotation.
Push-back LIFO racking
Here, there is just one loading and unloading area at the front of the structure, and the pallets are stored by pushing the previous ones towards the back of the racking.
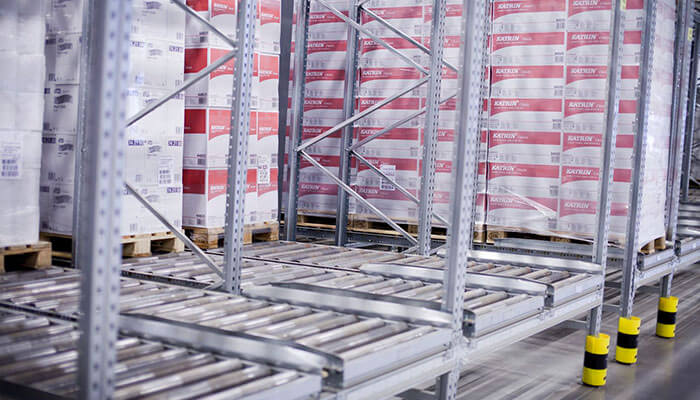
Crane racking
Crane racking is a fully automated storage system, ideal for storing pallets and large items.
Designed to work within very narrow aisles and at a height of more than 30 metres, crane racking is an efficient, optimised storage solution.
Guided by a management software system, the crane travels along the aisles of the warehouse, where it enters, positions and extracts the goods.
For multi-deep configurations, crane racking is equipped with a shuttle which retrieves the pallet and delivers it directly to the front, ensuring maximum accessibility.
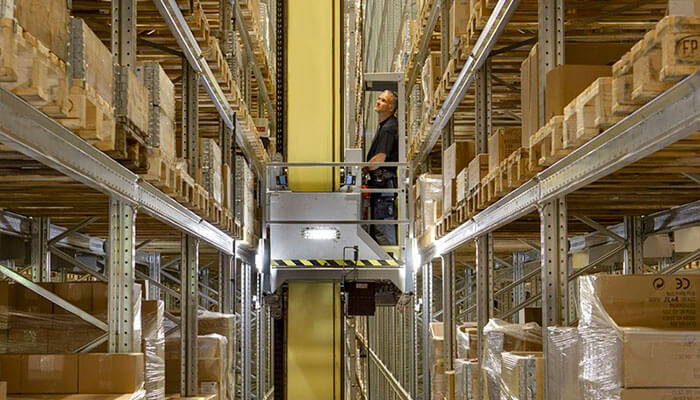
Multi-tier pallet racking
Multi-tier pallet racking introduces different levels to the warehouse, with varying heights of floors and aisles, all of which help make best use of the vertical space available.
Each different floor level can be accessed by stairways, and are linked by walkways. On each level a system of shelving is created for the different types of products.
Multitier shelving is particularly useful for businesses selling small products, such as pharmaceuticals or spare parts, that need to be hand-picked.
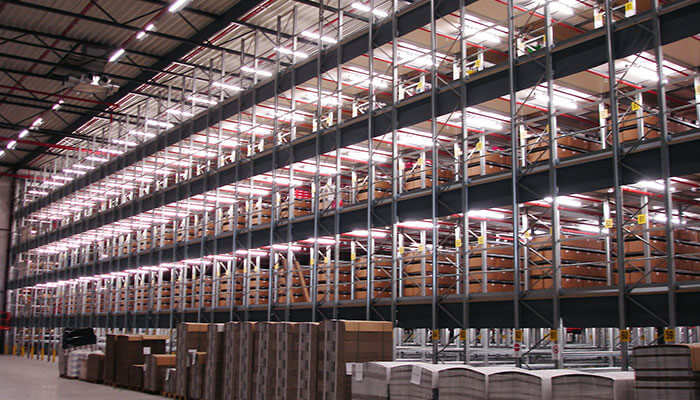
In this article we’ve covered the basic types of racking but there are many variations. The beauty of a warehouse which is well-equipped with the right systems is the ability to expand the range and add additional racking solutions as the business grows.
For more help and advice on how to find and implement the right storage solutions in your warehouse and boost performance, please get in touch.